氯化鈣經(jīng)熔鹽電解產(chǎn)出金屬鈣的過程,是工業(yè)上生產(chǎn)鈣的主要方法,包括氯化鈣制取和氯化鈣熔鹽電解兩大環(huán)節(jié)。氯化鈣熔鹽電解較早采用接觸陰極法電解,后來改進(jìn)用液體陰極法電解。
液體陰極法電解
以含鈣10%~15%的銅鈣合金液體作陰極,石墨電極作陽極,電解氯化鈣熔體制取富含鈣的鈣銅合金的過程。產(chǎn)出的鈣銅合金經(jīng)蒸餾獲得金屬鈣。
使用銅鈣合金作陰極,可在較低的電解溫度(973K以下)下制得含鈣65%的鈣銅合金(含鈣范圍較寬)。鈣銅合金中的鈣用蒸餾法很容易與銅分離。蒸餾殘余物即所謂貧合金,返回電解過程循環(huán)使用。由于鈣銅合金含鈣65%)的密度比電解質(zhì)小,始終留在電僻槽底部,不會漂浮到電解質(zhì)表面。
液體陰極法電解生產(chǎn)鈣銅合金,可以采用單一氯化鈣作電解質(zhì),但生產(chǎn)中廣泛采用易熔和導(dǎo)電性好的由無水CaCl2 和KCl組成的混合電解質(zhì)。隨著電解的進(jìn)行,電解質(zhì)中的CaCl2 含量不斷降低,需要定時(shí)往電解槽中補(bǔ)充新的無水CaCl2 ,以保持電解質(zhì)水平。
液體陰極法電解生產(chǎn)鈣的電流效率為72%,電能效率為30%,就是說有70%的電能消耗在電解槽的熱損失和被廢氣帶走的熱損失的補(bǔ)償上。電解時(shí),金屬鈣從槽底析出,在電解液層下面形成鈣銅合金,此時(shí)的電流效率隨陰極和陽極電流密度的增加而提高。這是因?yàn)殡S著電流密度的增加,電流的無用消耗損失相對變小,即電流的利用率提高。但是隨著電流密度的增加,電壓也增大,電能消耗增加。極間距增大,電流效率也隨之增加,因?yàn)闃O間距增大,鈣與從陽極上析出的氯氣發(fā)生的二次反應(yīng)也會減弱。增大極間距和增大電流密度都會同樣引起槽電壓升高,*終導(dǎo)致電能消耗增大。因此,電流密度和極間距之間應(yīng)保持一個(gè)*佳值。電流密度直接影響到電解析出的鈣量。當(dāng)電流密度過大,電解析出鈣的速度超過鈣向鈣銅合金的擴(kuò)散速度時(shí),鈣便會上浮到電解質(zhì)液面并發(fā)生氧化燃燒,導(dǎo)致電流效率降低。在實(shí)際生產(chǎn)中,陽極電流密度一般控制在1.7~3.25A/cm2 。電解質(zhì)中的水、NaCl、MgCl2 等雜質(zhì)也會使電流效率降低。
液體陰極法生產(chǎn)鈣采用矩形鑄鐵電解槽。為減少熱損失,槽與外殼之間砌有絕緣的保溫耐火磚。電解槽陽極由200mm×200mm×700mm的石墨塊組成,陽極塊用拉緊螺絲固定在金屬橫架上,電流通過軟母線導(dǎo)向陽極,軟母線則用壓板固定在橫架上,旋轉(zhuǎn)電解槽側(cè)部的手輪就可用于升降陽極。電解槽的上部蓋有多塊石棉水泥板。氯氣由電解槽內(nèi)經(jīng)過電解槽端部的豎煙道導(dǎo)向電解下面的集氣煙道,并從通風(fēng)機(jī)抽出,經(jīng)吸收塔處理后排入大氣。電解槽的電流強(qiáng)度為10000~40000A,并有增大的趨勢。鈣電解生產(chǎn)一般由多臺電解槽串聯(lián)而成。
一個(gè)或幾個(gè)以及一系列電解槽在安裝或大修之后,需要重新啟動(dòng)。電解槽啟動(dòng)之前要用木柴烘烤2~3h,以除去水分。烘烤后徹底清除槽內(nèi)灰渣,然后裝入40~50kg預(yù)先經(jīng)凈化和干燥的電解銅或60~70kg貧合金。在電解槽底均勻地敷上一層銅塊,調(diào)整陽極至陽極底面與銅層之間的距離不大于1cm。在電解槽壁和陽極之間的空間內(nèi)填充200~250mm厚的由80%~85%CaCl2 和15%~20%KCl組成的物料,并注入50~60kg熔融電解質(zhì)后,接通電源開始電解。當(dāng)鈣銅合金液面升至14~12cm時(shí),合金富集過程結(jié)束。合金中鈣含量在62%~65%時(shí),便由槽內(nèi)取出,但須保持有5cm深的電解液。富集的鈣銅合金取出后送去蒸餾。
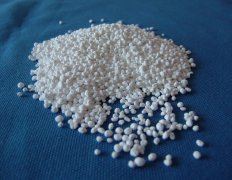